Load Cells Replacing Low-Accuracy Hydraulic Sensors in Mobile Industrial Applications
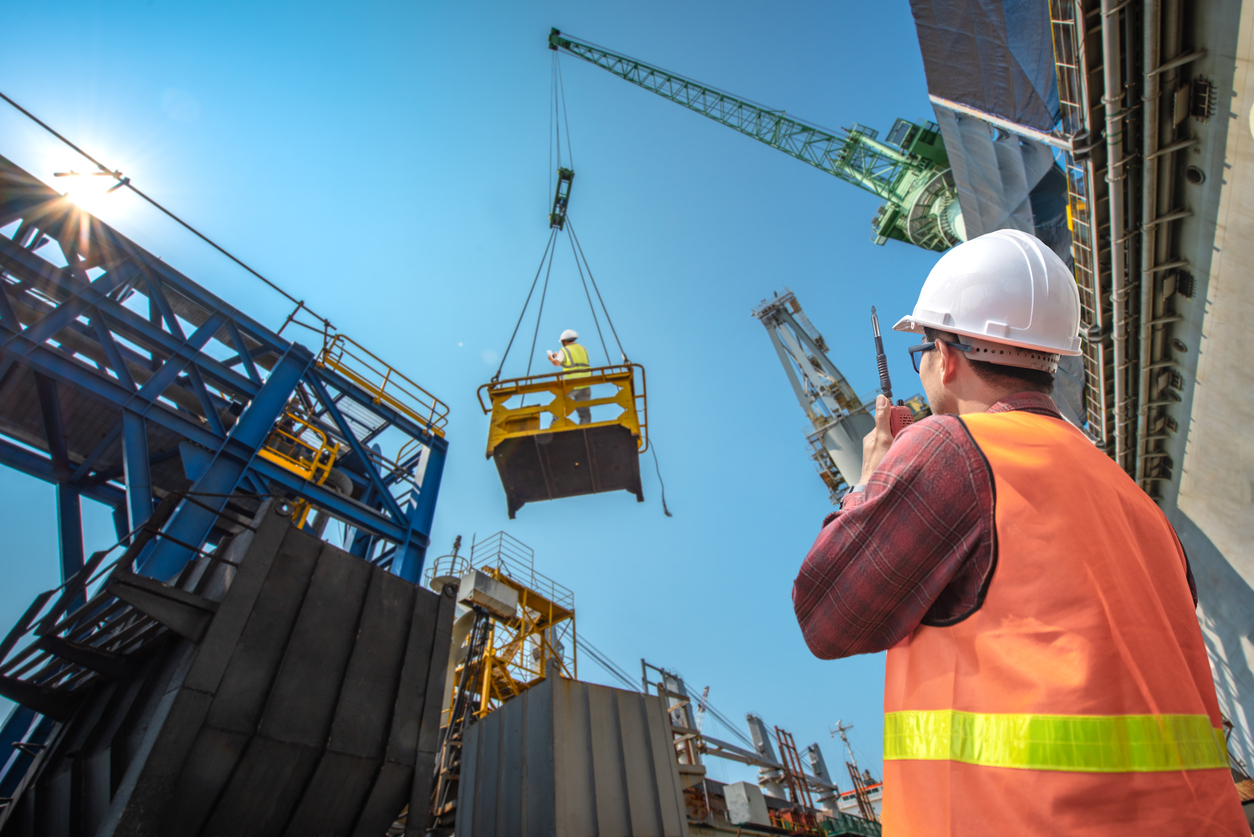
Precision matters, and close-enough estimations of aging hydraulic pressure transducer technology no longer deliver.
Modern manufacturers, OEMs, and system integrators increasingly choose load cells over pressure transducers as their preferred method of providing force feedback to the control systems within hydraulic machinery.
Load cells boast tighter performance specifications and directly capture forces output in mobile industrial equipment such as tractors, mobile lift platforms, cranes, forklifts, and more.
High-precision load cells directly convey critical force and weight information compared to indirect and less accurate hydraulic systems.
While hydraulic systems may still have limited applications, electronic load cell technology offers more applications for capturing data for more informed decisions.
We look at both transducer systems here and outline the benefits of load cell technology over hydraulic transducer feedback.
What are a Load Cell and Force Transducer?
Load cells instantly convert forces and weight into readable electric signals. These devices relay the change in electrical resistance as direct mechanical forces such as tension, pressure, torque, and compression are applied or removed.
It happens fast, and load cells measure it all with a high degree of accuracy.
Examples of Applications
A worker on a scissor lift must know instantly if the equipment nears maximum capacity. A forklift operator may need to know the specific weight of materials without requiring a freestanding scale.
Many mobile systems and equipment can incorporate load cells. Some examples beyond cranes and lifts include:
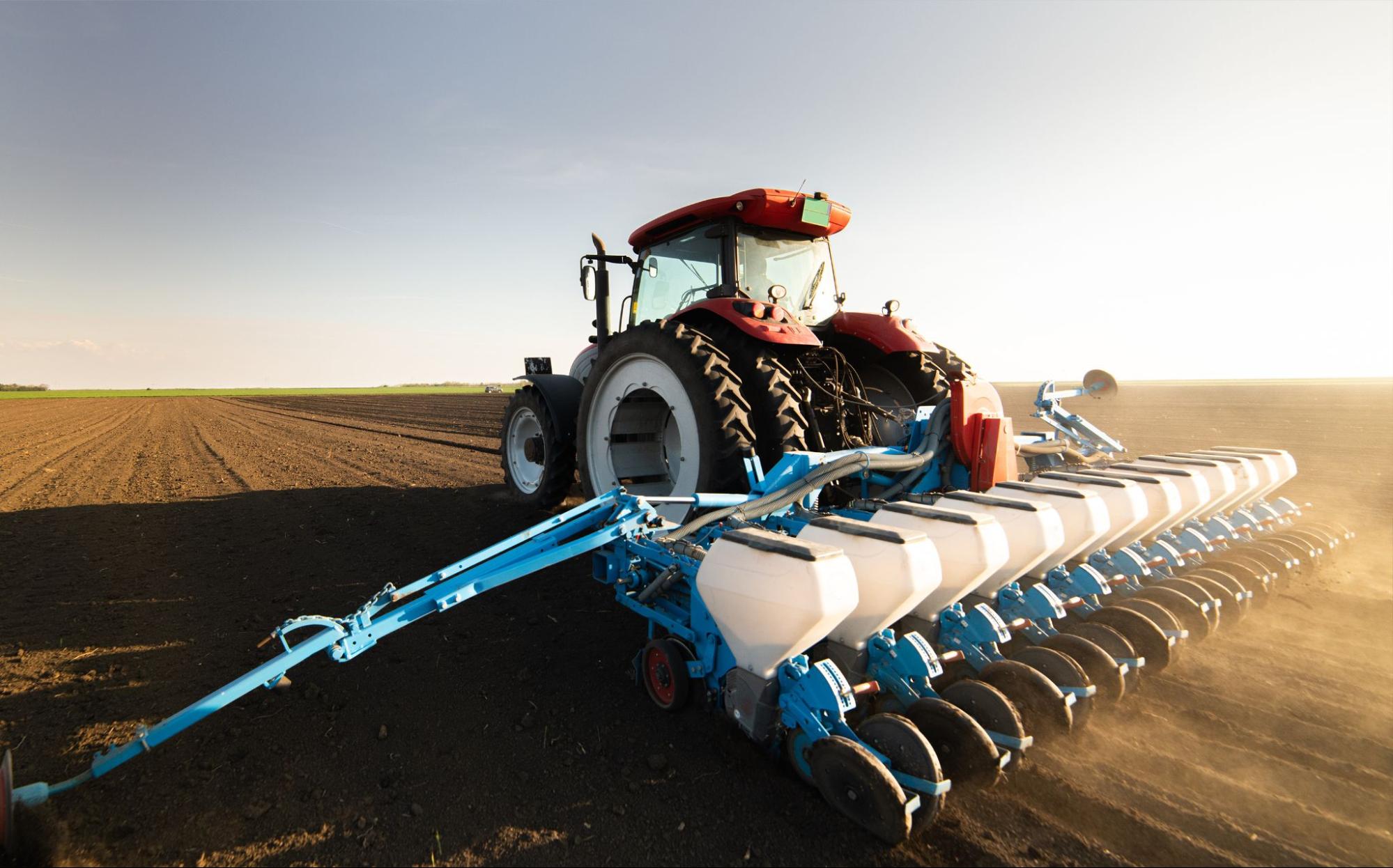
- Crop harvesting systems weigh grains in real-time
- Tractor draft control ensures proper blade depth and efficient engine operation
- Vehicle stability tracking to avoid tipping
- Drilling and filling equipment for aerospace manufacturing
- Mobile physical rehabilitation equipment
- Automated conveyor systems weighing, sorting, and packaging
Any delay or lack of precision poses a severe risk. Patients may be injured, and companies could suffer from inaccurate conveyor weighing.
Once calibrated for an industrial application, digital or analog systems display the information. The signal can trigger warnings or secondary operations through digital I/O processes.
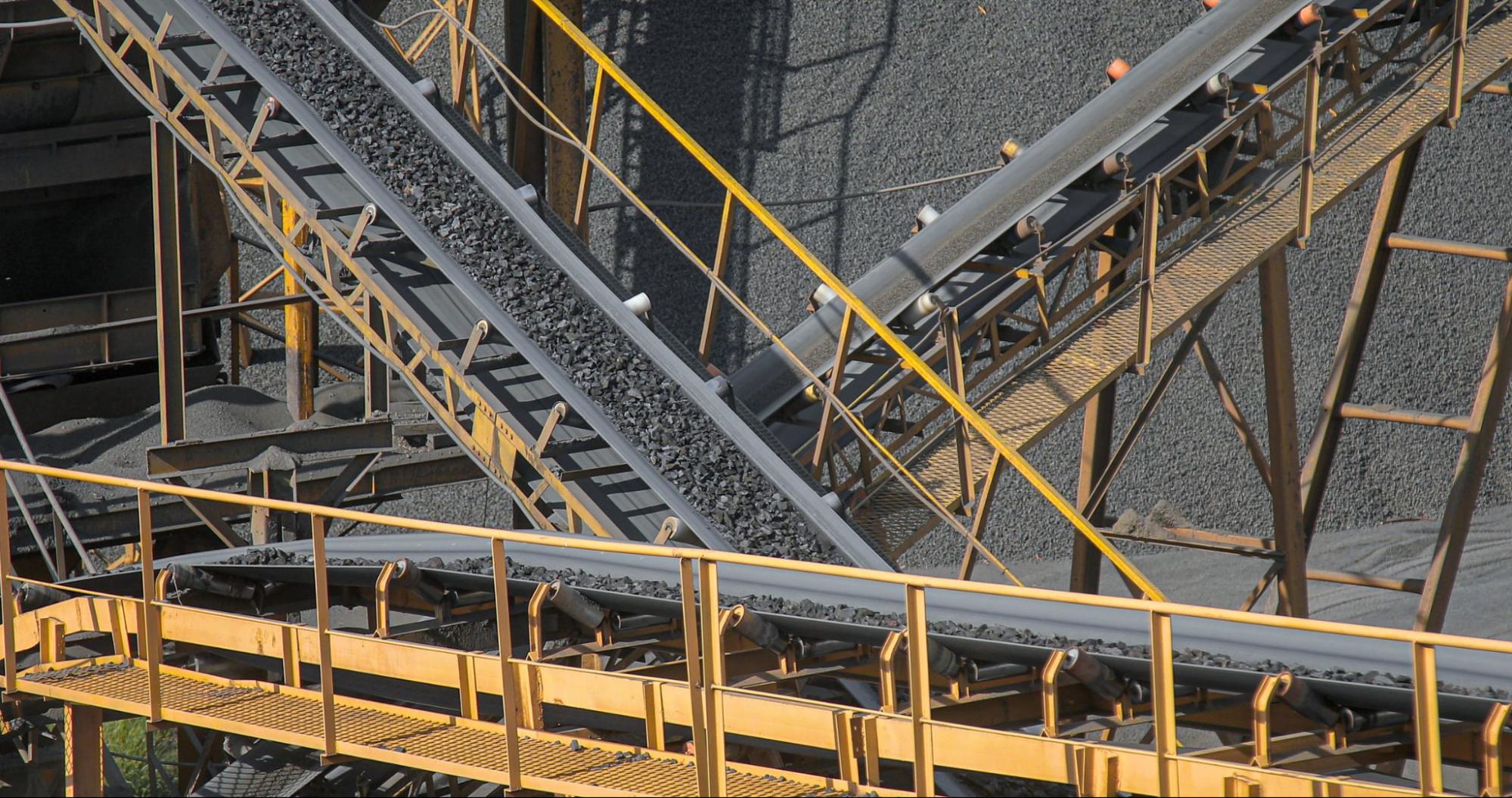
Many load cell designs monitor dynamic systems to deliver accurate readings rapidly. The choice of a particular load cell design depends on the application.
- Load Pin – Optimal for tractor hitches, lifts, and overhead weighing systems.
- Pancake – Integrates with stability systems.
- Bending Beams and Single-Ended Beams – Often used in belt or conveyor weighing equipment.
- S Beam – Supports suspending weighing systems, including patient lifts or industrial hoists.
These are some of the most common force transducers for mobile industrial applications.
Companies like Transcell engineer complex integrations using load cells that initiate functions based on predefined criteria.
What is a Hydraulic Load Cell?
The hydraulic load cells measure force indirectly using a hydraulic piston filled with hydraulic fluid. The application of load or force causes a pressure change in the fluid and position of the piston. This force change displays on an attached pressure gauge. All the components of the hydraulic force measurement are mechanically connected.
The Challenges of Using Hydraulic Systems
In cases where only coarse control is required, hydraulic pressure transducers can be used to provide load feedback. They do so by estimating force values, rather than measuring them directly.
This method of indirect load measurement with a hydraulic system introduces uncertainty, especially in systems that rely on fast and accurate responses. Some other drawbacks of hydraulic systems include:
-
Hydraulic systems are not very accurate
The indirect measurements create a wider margin of error. Internal friction in the system contributes to inaccurate readings. Also, contamination of the fluid is high. Once the fluid is contaminated, the accuracy drops drastically.
-
Measurements have low repeatability
Consistency and repeatability are essential for measuring force. Hydraulic systems lack fluid pressure compensation, making the systems vulnerable to external forces, including friction, nominal piston diameter, and backpressures.
-
Hydraulic systems are highly subject to ambient temperature
Variations in air temperature and humidity, which are difficult to control in industrial settings, affect the accuracy of hydraulic systems. Temperature changes within the hydraulics also affect measurement accuracy.
-
Latency in the measurement
Measurement with a hydraulic system depends on several dependent components – the piston, diaphragm, gauge, etc. that delay signal processing and delivery. The applied load must propagate backward through the hydraulic fluid (as an acoustic wave) before reaching the pressure transducer, creating a time lapse between the loading event and when the measurement is captured.
Some Applications Require Less Precision
Industries that don’t require the speed and accuracy of force transducers continue using hydraulic systems such as industrial presses, shock tubes, hydro-control, and automotive presses. Many mobile industrial applications require greater accuracy.
The Benefits of Load Cells for Mobile Applications
Load cells produce precise and fast measurements. Their size and accuracy make them a reliable choice for real-time information.
These are some of the benefits of using load cells in mobile industrial equipment applications.
-
System Automation
The relative size to function makes load cells the better choice for engineering many mobile machinery and equipment. Force transducers support greater operational efficiency when integrated with signal processing.
-
Measurements Without Delay
Unlike other sensors, load cells offer real-time information that meets mobile industrial demands without compromising precision.
-
Better data for Better Decisions
The load cell signals can be integrated into monitoring systems for data collection for real-time decisions. Draft control in tractors relies on load cells for monitoring plow strain to regulate engine power and optimal plowing depth.
-
Repeatable and Consistent Data
Force transducers measure load directly with dependability without needing pistons, fluids, hoses, and cylinders. Calibrations and setting of load units can be done with data collected from load cell integrations.
The added error and latency of a pressure-based feedback signal ultimately degrade the potential performance of the control system. Load cells capture force measurements directly and avoid these pitfalls. This dramatically improves the accuracy of the measurement while also delivering measurements that are realtime.
Choosing Solutions, Not Just a Supplier
There’s a lot at stake with your equipment and for equipment operators – safety, efficiency, stability. Look for strain gauge components solutions from a company that differentiates itself as more than a commodity distributor. You’ll have confidence in the recommended solutions from a company with a history that combines manufacturing and engineering.
- Customization of both sensing technology and connected electronic components
- Able to make your force measurement solution fit your equipment instead of modifying equipment to provide the solution
- Primary engineering services offered in the U.S.
- Sources the highest quality materials and components
- Integrated manufacturing and engineering for end-to-end solutions
- Tested for precision and reliability
Schedule a Free Consultation with Transcell
Close Enough Can’t Cut it Anymore
Manufacturers, OEMs, and integrators demand high precision and durability. Load cells and force transducers offer that dependability in critical equipment and operations.
If something can be measured, it can be controlled as long as the information is accurate.
Force transducers deliver information of greater value.